1. Preface of electrode electroslag surfacing:
The inner surfaces of reactors, reactors and thick-wall pressure vessels of nuclear power plants in the petrochemical industry require large area surfacing welding of stainless steel linings that are resistant to high temperature, oxygen and hydrogen sulfide corrosion. In the 1970s, in this field, a large number of domestic and foreign use of electrode submerged arc surfacing (SAW) technology. The width of the band pole is also developed from narrow band to 60mm, 90mom, 120mm, 150mm broadband direction. This technology has made great progress in dilution rate and deposition speed compared with submerged wire arc welding.
However, with the increasing size and high parameterization of pressure vessels, surfacing welding technology has been developed in a higher quality and more efficient direction. electrode electroslag surfacing ,Electroslag surfacing technology with electrode has been developed rapidly and widely in recent years because of its advantages of higher production efficiency, lower dilution rate and good weld formation than that of submerged arc with electrode.
Electrode electroslag surfacing is a highly efficient surfacing method, which is divided into two types: electrode submerged arc surfacing and electrode electroslag surfacing. Due to the use of thin plate type wide electrode and high welding current, so its melting speed is more than ten times to dozens of times of various monofilm welding melting speed.
2. One of the differences between Submerged Arc Strip Cladding (SASC) and common submerged arc welding SAW is that the welding wire is changed to a strip electrode. The arc is created between the strip pole and the workpiece. Flux flux is used to form a slag to protect the weld pool and help form a smooth weld surface.
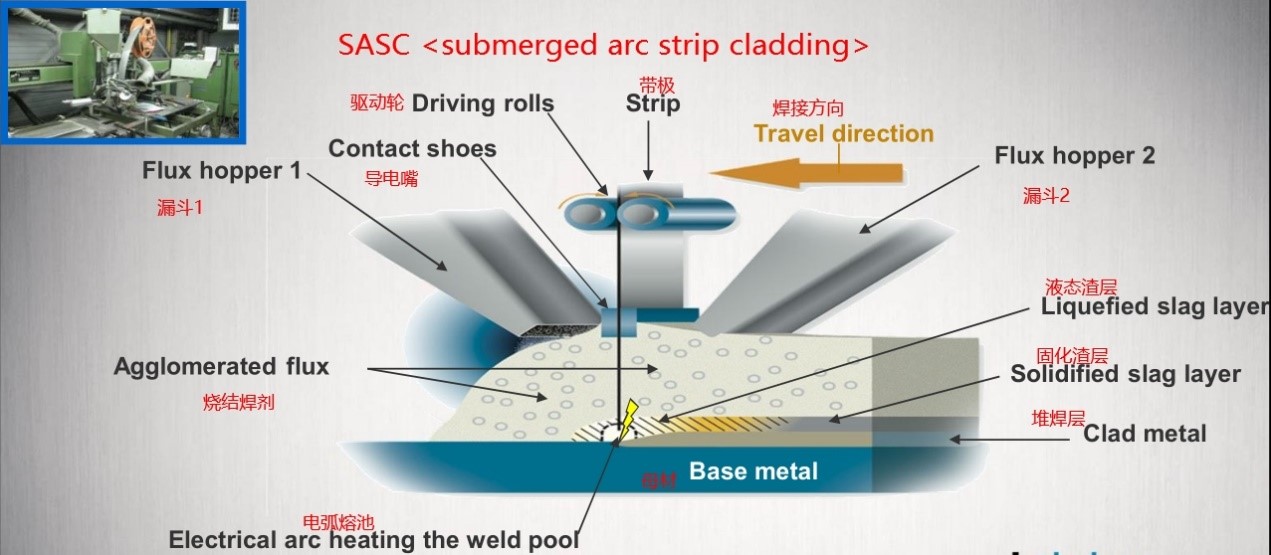
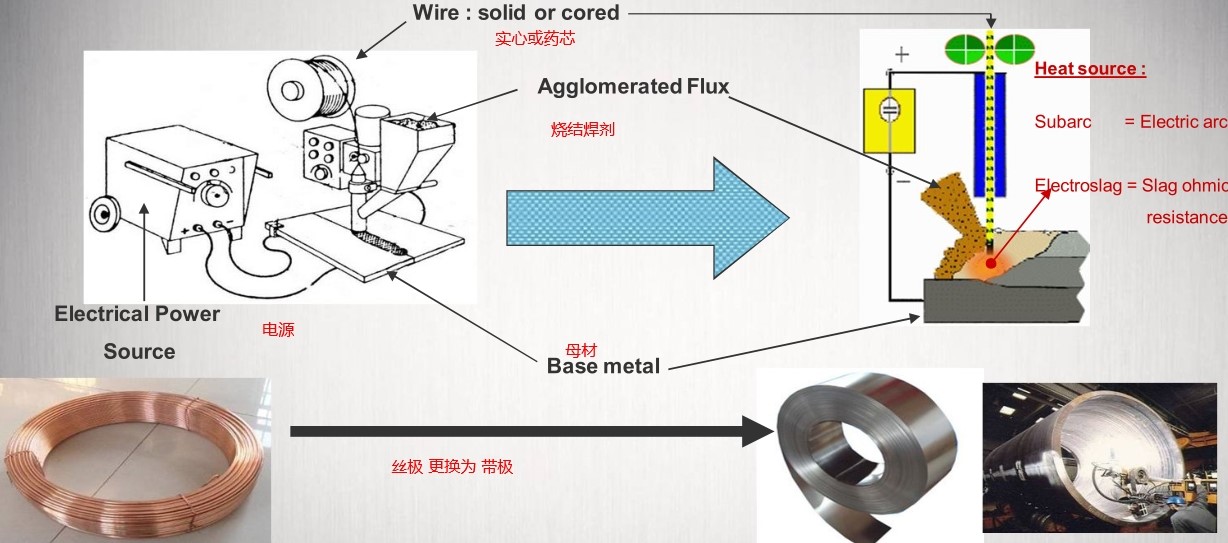
3. Electrode electroslag welding
Electrode electroslag surfacing is the resistance heat caused by the liquid slag as a heat source. First, the arc is ignited between the electrode and the base material. The heat generated by the slag melts the surface of the substrate, and the edge of the electrode is immersed in the slag and flux. After the arc heat melts the flux to form the slag pool, the arc heat transitions to the resistance heat of the slag. The melted metal has a high density and sinks to form a liquid metal molten pool. The slag has a low density and floats above the molten pool. The slag pool is covered with the metal molten pool to protect the metal molten pool. Then the electrode continues to melt, the liquid metal and slag in the molten pool are rising continuously, and the lower liquid metal far away from the heat source is cooled and condensed into a surfacing layer.
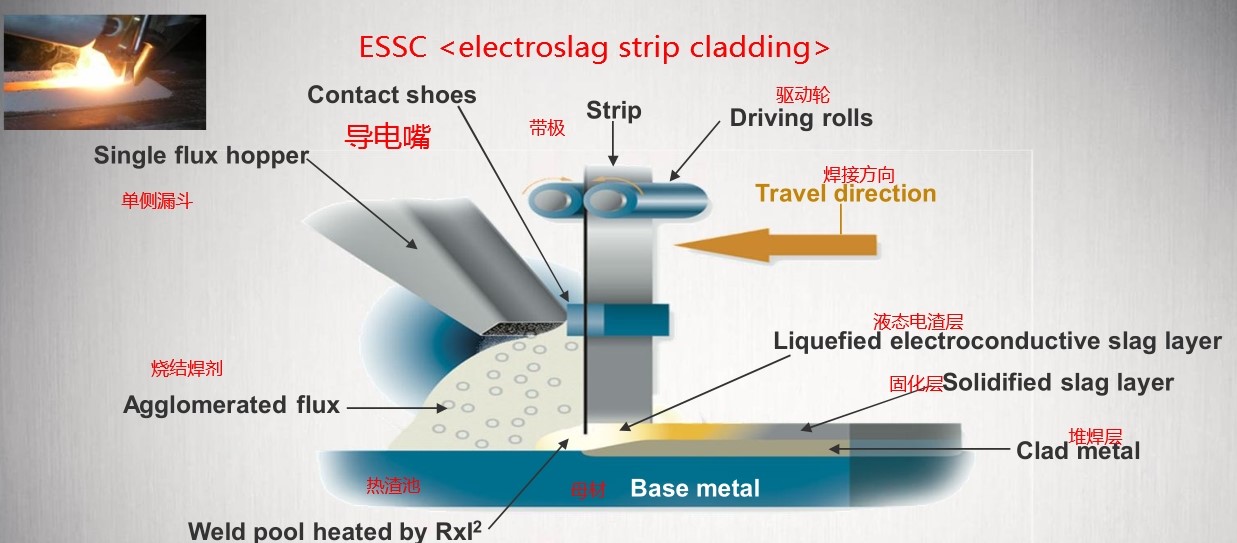
Compared with submerged arc surfacing with pole, ESW or ESSC has the following characteristics:
ALSO IS electrode electroslag surfacing.
(1) The melting rate was increased by 60%-80%. (See picture below)
(2) Because the penetration is very shallow (about 10% to 15% dilution rate), only half of it is diluted to the base material.
(3) Welding low voltage (24-26 V).
(4) Large current and current density (60mm wide welding belt through the current is l000-1250A, the corresponding current density is 33-42 A/mm2), especially the high-speed flux allows the welding current to exceed 2000A, the corresponding current density is 70 A/ram2.
(5) The welding speed is increased (50%-200%), resulting in an increase in the coverage area.
(6) The heat input is roughly the same.
(7) Low flux burn loss (about 0.4-0.5kg /kg strip).
(8) The curing rate of ESW welding weld metal is very low, which is conducive to porosity escape and reduce porosity defects. Oxygen can escape from the molten electroslag pool to the surface; The metal surface of the surfacing layer is quite clean, which reduces the tendency of thermal cracking and intergranular corrosion from a metallurgical point of view.
In the practical application of industrial production, electrode electroslag surfacing is very important that the weld surface of the product has a higher melting rate and a lower dilution rate than the base metal. Submerged arc surfacing with electrode has been widely used in large surface surfacing, but electroslag surfacing technology is gradually taking the dominant position.
Electrode electroslag surfacing mainly used in petrochemical machinery, engineering machinery, wind power equipment, construction & bridge, shipbuilding, food & pharmaceutical and other industries